1. 原材料带入
商品混凝土由水泥、砂石、水及外加剂等原材料组成。在砂石采集、运输及堆放过程中,难免会有土壤杂质混入。这些微小的土壤颗粒在搅拌过程中未能完全分离,最终随混凝土一起被浇筑,导致混凝土表面粘土。
2. 搅拌不均匀
混凝土搅拌是确保各组分均匀混合的关键环节。若搅拌时间不足或搅拌设备性能不佳,易导致土壤等杂质未能充分分散,从而在混凝土中形成局部聚集,造成粘土现象。
3. 运输过程中的污染
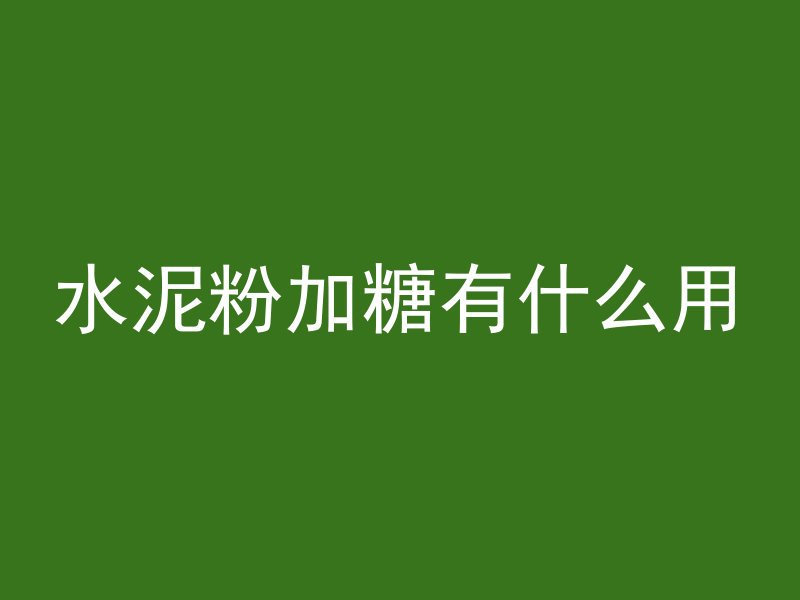
在混凝土从搅拌站运输到施工现场的过程中,若运输车辆清洁不当或密封不严,外界的土壤、灰尘等易通过车辆缝隙进入混凝土中,导致粘土问题的出现。
4. 施工环境因素
施工现场的环境条件也是影响混凝土粘土的重要因素。如遇到风沙天气,空气中的尘土易附着在混凝土表面;而地面上的泥土也可能在浇筑过程中被带入混凝土中。
5. 模板清洁度不足
混凝土浇筑前,模板的清洁度至关重要。若模板表面残留有土壤、油污等杂质,这些杂质在混凝土浇筑时会与混凝土接触,从而造成粘土现象。
6. 振捣不充分
在混凝土浇筑过程中,振捣是确保混凝土密实度的关键步骤。若振捣力度不足或振捣方式不当,易导致混凝土内部的气孔和空隙未能充分排出,土壤等杂质也可能因此残留在混凝土表面。
7. 养护不当
混凝土浇筑完成后,适当的养护对于其性能至关重要。若养护过程中未能及时清理混凝土表面的土壤等杂质,这些杂质将随着养护的进行而更加牢固地附着在混凝土上。
8. 外加剂影响
某些外加剂(如减水剂、引气剂等)的加入可能会改变混凝土的工作性能,包括其粘稠度和抗离析性。这些变化有时会导致土壤等杂质更易附着在混凝土表面。
9. 水灰比控制不当
水灰比是混凝土配合比中的重要参数。若水灰比过大,混凝土的粘稠度降低,土壤等杂质更易随混凝土流动而附着在其表面;反之,若水灰比过小,混凝土过于干硬,也不利于杂质的分离。
商品混凝土表面粘土的原因多种多样,涉及原材料、搅拌、运输、施工环境、模板清洁度、振捣、养护以及外加剂和水灰比等多个方面。为确保混凝土的质量与美观性,我们应从这些方面入手,采取相应措施减少或避免粘土现象的发生。例如,加强原材料的筛选与清洁、提高搅拌效率与均匀性、改善运输与施工环境、严格模板清洁与振捣操作、合理控制水灰比以及选用合适的外加剂等。通过这些措施的实施,我们可以有效提升商品混凝土的质量与施工效果。