在混凝土构件的制备过程中,气孔问题往往影响着构件的密实度与耐久性。为了减少气孔,提升混凝土质量,我们需要从多个方面入手,细致优化每一个生产环节。
1. 选用优质材料
应从源头上把控,选用高质量的水泥、骨料及外加剂。水泥的品质直接影响混凝土的水化反应,进而影响气孔生成。骨料需洁净、级配合理,以减少因骨料本身缺陷导致的气孔。外加剂的选择也至关重要,应选用能有效降低混凝土粘度、促进气泡排出的类型。
2. 严格控制配合比
合理的配合比是保证混凝土性能的基础。通过试验确定**的水灰比、砂率等参数,可以有效减少气孔的产生。过高的水灰比会导致混凝土内部孔隙增多,而合理的砂率则能确保混凝土拌合物的均匀性,有利于气泡的排出。
3. 加强搅拌工艺
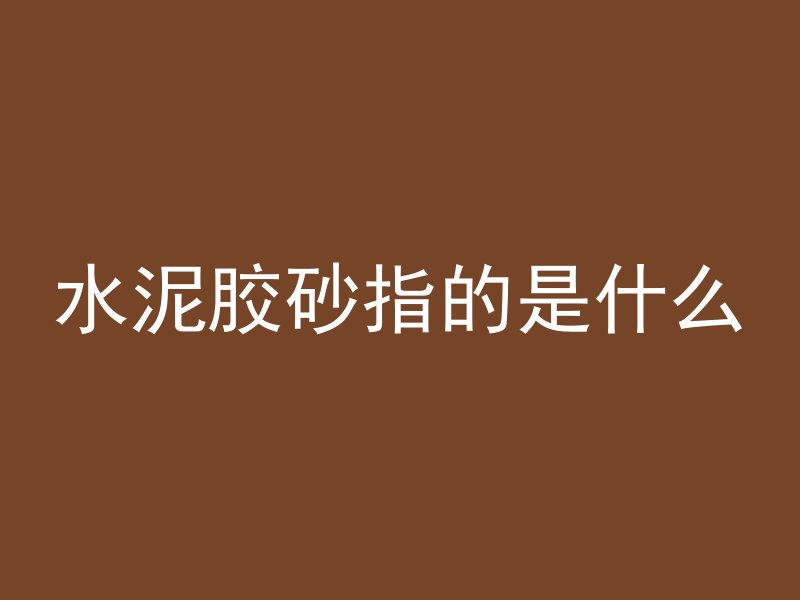
搅拌是混凝土制备中的关键环节。应确保搅拌时间充足,使各种材料充分混合均匀,避免局部出现干粉团或水分聚集,从而减少因搅拌不均导致的气孔。搅拌速度也需适中,过快可能导致气泡难以排出,过慢则影响混合效率。
4. 优化浇筑与振捣
浇筑时,应控制浇筑速度,避免混凝土产生分层或离析。振捣是减少气孔的有效手段,通过振捣可以促使混凝土内部的气泡上浮并排出。振捣应均匀、适度,过振可能导致混凝土分层,欠振则无法有效排除气泡。
5. 使用脱模剂与养护
选用合适的脱模剂可以减少模具与混凝土之间的粘结力,有利于气泡的排出。良好的养护条件也是减少气孔的重要因素。养护期间应保持混凝土表面湿润,避免因水分蒸发过快导致的气孔增多。
6. 控制环境温度与湿度
环境温度与湿度对混凝土的硬化过程有重要影响。过高的温度可能导致混凝土内部水分蒸发过快,形成气孔;而湿度过大则可能影响混凝土的干燥速度,进而影响其性能。应根据具体情况调整施工环境的温湿度条件。
7. 引入真空辅助技术
真空辅助技术是一种有效的减少混凝土气孔的方法。通过在混凝土浇筑后施加真空压力,可以促使混凝土内部的气泡快速排出,从而提高混凝土的密实度与耐久性。
8. 加强质量控制与检测
应加强对混凝土构件的质量控制与检测。通过定期检测混凝土的孔隙率、密实度等指标,可以及时发现并解决问题。建立严格的质量管理体系,确保每一道工序都符合标准要求。
减少混凝土构件气孔需要从材料选择、配合比控制、搅拌工艺、浇筑与振捣、脱模剂使用、养护条件、环境温度与湿度控制、真空辅助技术应用以及质量控制与检测等多个方面入手。只有综合考虑这些因素,才能有效减少气孔的产生,提高混凝土构件的质量与耐久性。