混凝土粉末石膏的合成是一个涉及多个步骤和技术的复杂过程。本文将详细介绍如何合成混凝土粉末石膏,从原料准备到成品产出,全面解析其关键环节。
原料准备
合成混凝土粉末石膏的首要步骤是精心挑选和处理原料。通常,选用上乘的天然石膏块或工业副产石膏作为原料。这些原料需经过破碎工序精细处理,确保粒度均匀,为后续步骤打下坚实基础。
煅烧工艺
煅烧是合成过程中的关键步骤。将处理后的石膏原料放入窑炉中,通过精准控制煅烧的温度与时间,使其发生化学变化,转化为所需的熟石膏。煅烧工艺的不同直接影响石膏粉的质量,因此必须严格控制煅烧条件。
粉碎与研磨
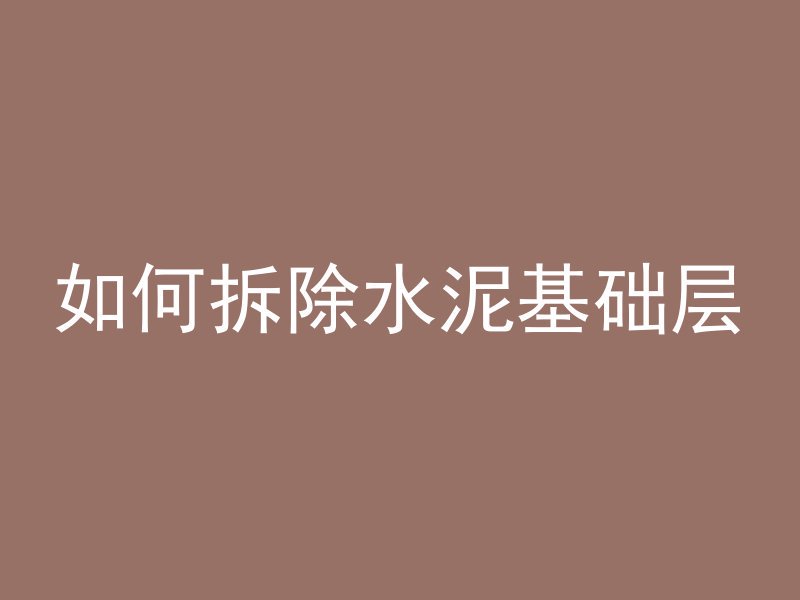
煅烧完成后的石膏块需进一步粉碎和研磨,以获得所需粒度的石膏粉。这一步骤通常采用先进的研磨设备,如球磨机、雷蒙磨机等,确保石膏粉粒度均匀,满足后续生产要求。
筛分与分级
研磨后的石膏粉需经过筛分机构进行分级处理,以确保粒度均匀达标。高效筛分机构能够精准分离出不同粒度的石膏粉,为后续混合和包装提供便利。
添加剂的加入
为优化石膏粉性能,如加快凝结速度、增强抗折抗压强度等,可加入改性高分子量聚乙烯纤维、乳白胶、复合缓凝剂等添加剂。这些添加剂能有效提升石膏粉的物理和施工性能,使其更适用于混凝土粉末的制备。
混合与均化
将经过筛分和分级的石膏粉与添加剂按一定比例混合均匀,是合成混凝土粉末石膏的重要步骤。这一过程需采用专业的混合设备,确保各组分充分混合,达到预期的均化效果。
成品包装与储存
混合均匀的石膏粉需进行包装并妥善储存。包装材料应具有良好的密封性和防潮性,以防止石膏粉在储存过程中受潮变质。储存环境也需保持干燥通风,确保石膏粉质量稳定。
环保与节能措施
在合成混凝土粉末石膏的过程中,还需注重环保与节能。采用余热回收、热能中心温度调节等技术降低能耗和排放,既环保又降成本。选用低能耗、高效率的生产设备也是实现绿色生产的重要途径。
自动化控制系统
引入自动化控制系统对生产环节进行精确控制和高效管理,能够显著提升生产效率和产品质量稳定性。通过自动化控制系统,可以实现对原料配比、煅烧温度、研磨粒度等关键参数的实时监控和调整,确保生产过程稳定可靠。
合成混凝土粉末石膏是一个涉及多个步骤和技术的复杂过程。通过精心准备原料、严格控制煅烧条件、采用先进的研磨和筛分设备、加入适量的添加剂以及注重环保与节能措施等措施,可以生产出高质量、高性能的混凝土粉末石膏。