在探讨混凝土抛光地面的工艺中,选择合适的抛光材料与技术至关重要,它不仅影响地面的最终效果,还关乎施工效率与成本。以下是对这一主题的深入剖析。
1. 抛光材料选择
混凝土抛光地面首先需考虑抛光材料的选用。常见的抛光材料包括金刚石磨片、树脂磨片及陶瓷磨片等。金刚石磨片因其硬度高,适用于粗磨阶段,能快速去除表面瑕疵;树脂磨片则更细腻,适合中磨和细磨,提升地面光泽度;而陶瓷磨片则兼顾耐磨与细腻,是终磨阶段的优选。选择合适的磨片组合,能显著提高抛光效率与质量。
2. 磨片粒度序列
抛光过程中,磨片的粒度选择需遵循由粗到细的原则。初期使用较粗的粒度(如30、60)去除混凝土表面的浮浆和不平整,随后逐步过渡到更细的粒度(如120、240),直至使用3000甚至更细的磨片进行终磨,以达到镜面效果。这一序列化的粒度选择,确保了抛光过程的连贯性和地面质量的逐步提升。
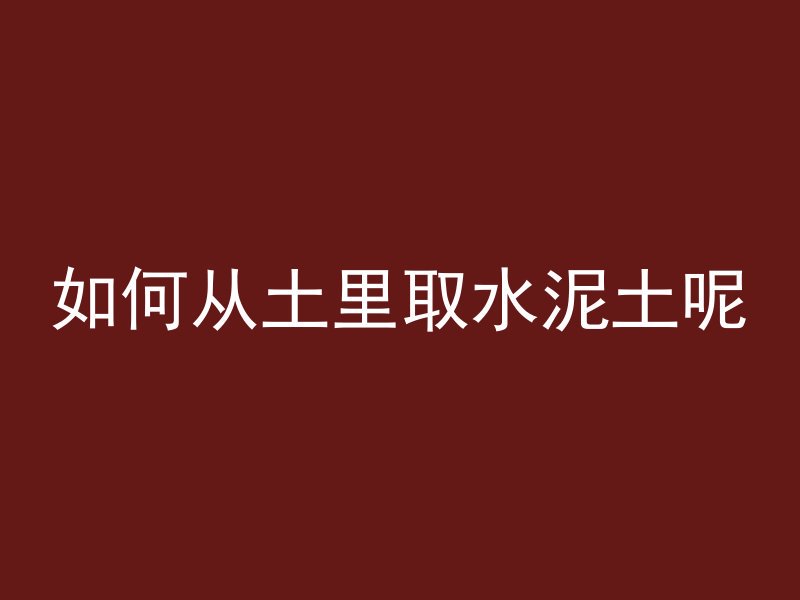
3. 抛光液的作用
抛光液在抛光过程中起着润滑、冷却和增强抛光效果的作用。它能帮助磨片更好地与混凝土表面接触,减少摩擦热,同时携带磨屑,保持磨片锋利。选择合适的抛光液,如水性或油性抛光液,需根据具体工况和抛光需求决定,以达到**抛光效果。
4. 设备选型
抛光设备的选择同样关键。手持式抛光机适用于小面积或边角处理,而大型自动抛光机则适合大面积作业,能显著提高施工效率。设备功率、转速及磨盘尺寸均需根据抛光需求和地面状况综合考虑,以确保抛光效果与施工效率的**平衡。
5. 施工技巧
抛光时,操作人员的技巧也直接影响抛光效果。保持匀速移动,避免停留过久导致局部过热;适时调整磨片压力,以适应不同硬度的混凝土;注意边角处理,确保整体美观。这些技巧的掌握,是提升抛光质量的关键。
6. 地面硬度要求
混凝土地面的硬度直接影响抛光效果。硬度过高可能导致磨片磨损加快,而硬度不足则难以达到理想的镜面效果。在施工前应对地面进行硬度测试,并根据测试结果调整抛光方案。
7. 养护与保护
抛光完成后,地面的养护同样重要。应定期清洁,避免使用酸性或碱性清洁剂,以免损伤地面。可涂抹保护剂,增强地面的耐磨性和抗污性,延长使用寿命。
混凝土抛光地面的成功实施,离不开对抛光材料、粒度序列、抛光液、设备选型、施工技巧、地面硬度要求以及后期养护等多方面的综合考虑与精细操作。通过科学合理的规划与执行,方能打造出既美观又耐用的抛光混凝土地面。